Open Innovation Submission Portal
Moisture Barrier for Flexible Packaging
Request Number 105450 | Author PepsiCo
Description
PepsiCo is looking for novel resins that can co-extrude with their core resins to form a skin layer with high functionality that can anchor metal to film or highly functional coatings which would serve the same purpose. Inherently high barrier coatings that can be applied as primer coating or top coating over metal could also be a solution.
Background
PepsiCo has been working on bio-based/biodegradable flexible films for food packaging to help achieve their sustainability goals of having 100% RCB (Recyclable, Compostable, Biodegradable) compliance for their packages as well as 20% reduction in GHG (greenhouse gas) by 2030. While flexible packaging is a very sustainable option from a material use point of view, the multi-layer multi-material structures are not conducive for recycling and mostly end up in the landfill or as litter. While biodegradable films help with the end-of-life issues by designing for managed waste infrastructures like composting and anaerobic digestion, it cannot be at the expense of performance compromises such as reduced shelf stability. Oxygen barrier is not a problem with these films but achieving extremely high moisture barrier required for packaging dry foods (< 0.3 g/m2/day under tropical conditions of 38C/90% RH) has been a challenge. PepsiCo understands that metallization will be needed to achieve the high moisture barrier requirements, but even with metallization PepsiCo has not been able to reach this barrier with bio-based films. Also, it is important to maintain this barrier under forming conditions in the VFFS process of bag-making.
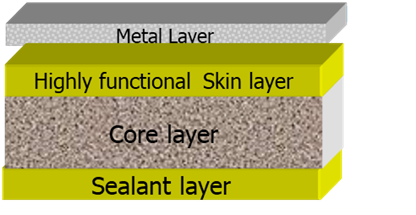
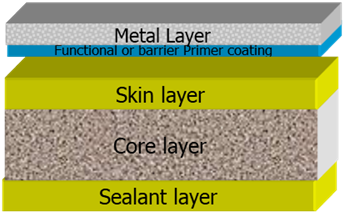
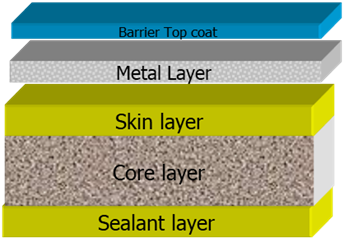
Key Success Criteria
Must-Have requirements
- Barrier skin resins should be co-extrudable with PLA/PHA resin in blown film or cast film processing conditions
- The barrier skin layer should have good adhesion to core layer, or a suitable tie layer needs to be identified
- The barrier resin should be biodegradable under home composting conditions at a minimum
- If barrier or metallization primer coating, it should be applicable on to our film by commercially available roll coating processes
- Possible to metallize on top of skin layer or coating
Nice-to-Haves
- The ideal solution would have all the Must Haves and all the Nice to Haves. Of the multiple technologies that meet all the Must Haves (minimum requirement) the one that meets the most Nice-to-Haves may be the best. Based on weighting factors the Nice to Have factors could be used to prioritize similar solutions.
- The skin layer option is preferable as it enables avoiding a unit operation in the conversion cycle
- Identification of barrier options (both skin and coating) which could help avoid metallization would be ideal (stretch goal)
- Solvent-free coating technology is ideal from a GHG point of view but willing to try both water-based and even solvent-based technologies
- Recent advances in metallization with other metals like silicon etc. are welcome
Approaches not of interest
- Solvent cast film technologies would not be commercially available
- PGA, G-polymer as skin resins
- Nano-cellulose, nano-clay coatings but recent advances are welcome
Preferred Collaboration types
PepsiCo is open to a variety of engagement types:
- sponsored research for development and proof of concept testing,
- consultation
- licensing existing technology for PepsiCo to apply
- purchase commercial ready solution, open to any, etc.
© PepsiCo. All Rights Reserved. Privacy Policy | Terms of Use | Contact Us